A recent report by a failure review board has identified a malfunctioning pressure control valve (PCV) as the primary cause of the propellant leak that prevented Astrobotic's Peregrine lunar lander from reaching the moon in January. The valve failure led to a loss of helium pressurant, causing the oxidizer tank to rupture and rendering the spacecraft unable to attempt a lunar landing.
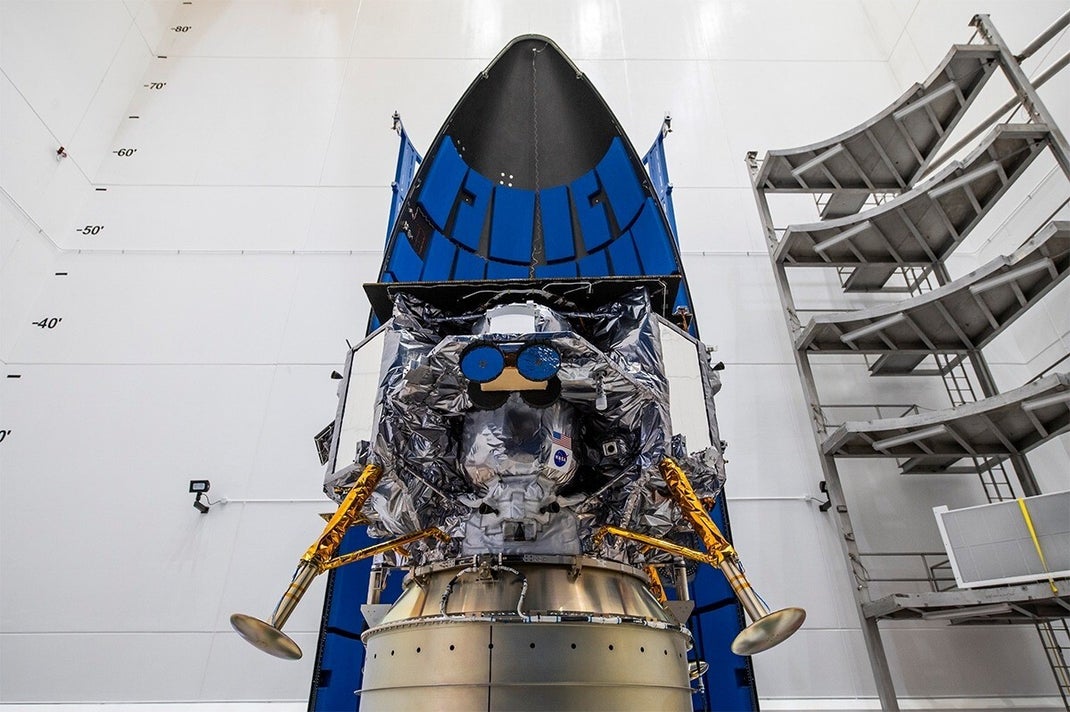
Astrobotic’s Peregrine lunar lander attached to the payload adapter for ULA’s Vulcan Centaur launch vehicle. Credit: ULA
The Peregrine lunar lander was launched on January 10, 2024, aboard a United Launch Alliance (ULA) Vulcan Centaur rocket from Cape Canaveral Space Force Station, Florida. The launch vehicle performed nominally, injecting the spacecraft into a lunar transfer orbit. However, approximately 24 hours after launch, mission controllers detected a propellant leak, which was later determined to be caused by the malfunctioning PCV2 valve.
The investigation revealed that the valve had worked normally during prelaunch testing but failed after launch due to "vibration-induced relaxation" in threaded components. This caused a mechanical failure in the valve, preventing it from sealing properly.
Further analysis showed that the valve's failure was attributed to a phenomenon known as "thread creep," where the repeated vibration and stress on the valve's threads caused them to relax and lose their sealing properties. This resulted in a leak rate of approximately 0.1 kg/s, which was sufficient to
drain the oxidizer tank and render the spacecraft unable to perform its lunar landing mission.
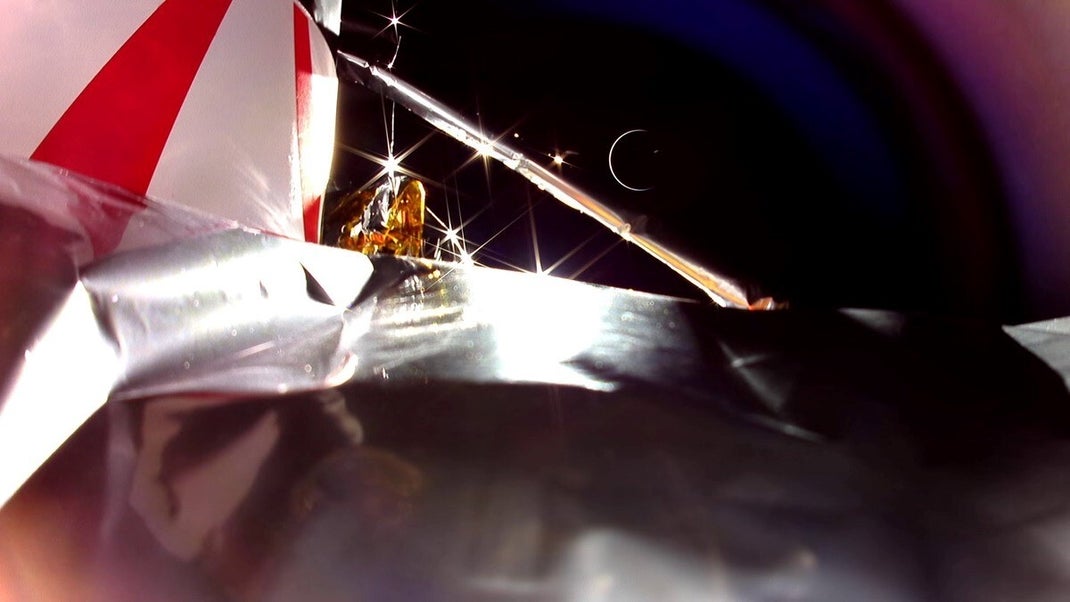
One of the last images returned from Astrobotic’s Peregrine lander was this view showing the crescent Earth as the spacecraft neared reentry. Credit: Astrobotic
The review board's report also highlighted several contributing factors, including:
1. Insufficient testing: The PCV2 valve had not been subjected to sufficient vibration and acoustic testing prior to launch, which may have revealed the thread creep issue.
2. Design limitations: The valve's design did not include a redundant sealing mechanism, making it more susceptible to failure.
3. Material selection: The valve's materials may not have been suitable for the harsh conditions of space, contributing to the thread creep phenomenon.
As a result of the findings, Astrobotic is redesigning the valve and implementing changes to the propulsion system on its larger Griffin lander, set to launch by the end of 2025. The company is working with the valve vendor to develop a new design that includes:
1. Redundant sealing mechanisms
2. Improved materials selection
3. Enhanced testing protocols
Additionally, the Griffin lander will feature a regulator to control the flow of helium used to pressurize the tank, as well as backup latch valves to prevent a similar failure.
Add comment
Comments
Boeing happen to make those valves?